How to Design Dust Collection and Ventilation System for Pharmaceutical Cleanroom?
- Share
- Issue Time
- Mar 14,2024
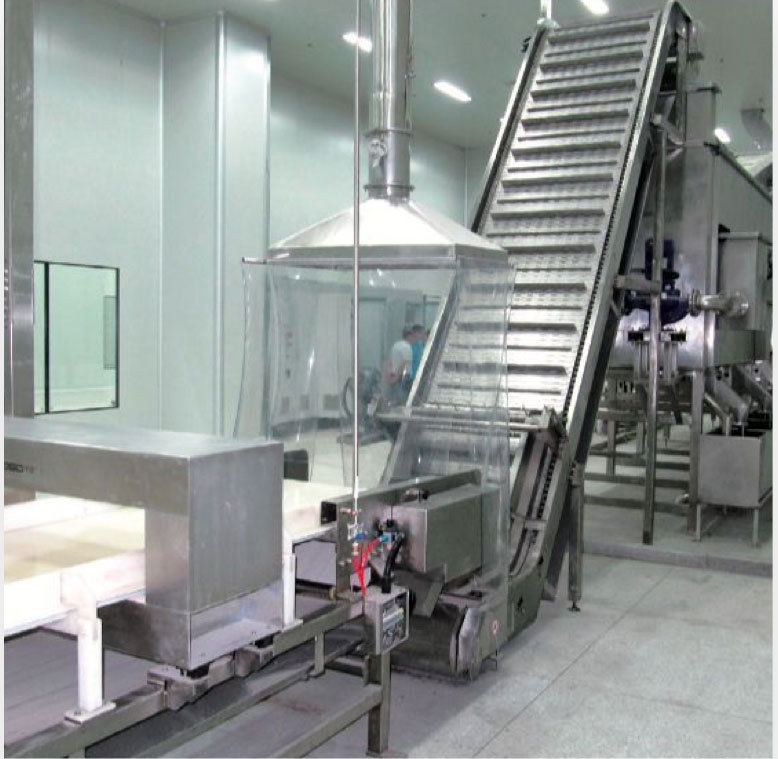
How to Design Dust Collection and Ventilation System for Pharmaceutical Cleanroom?
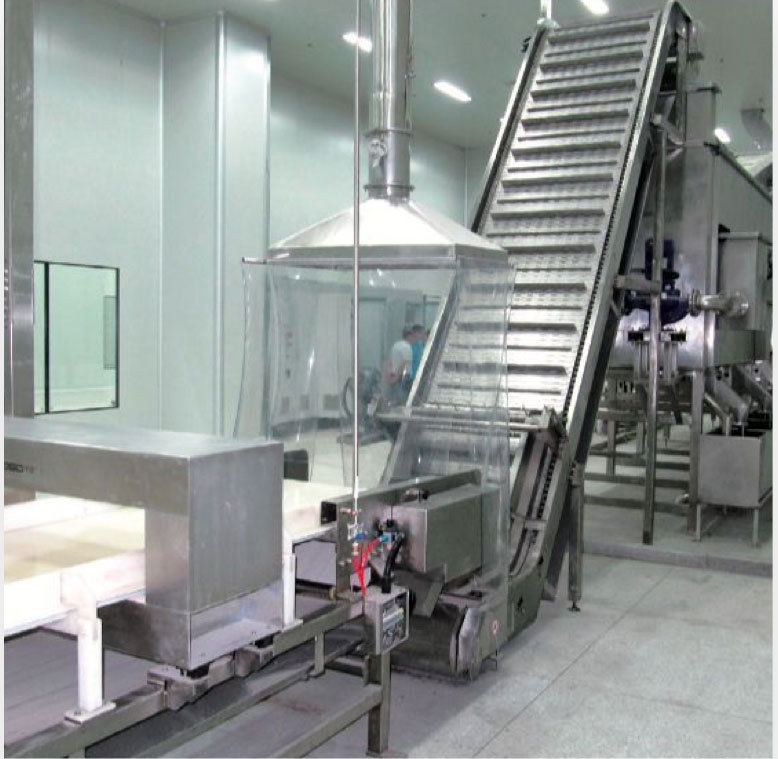
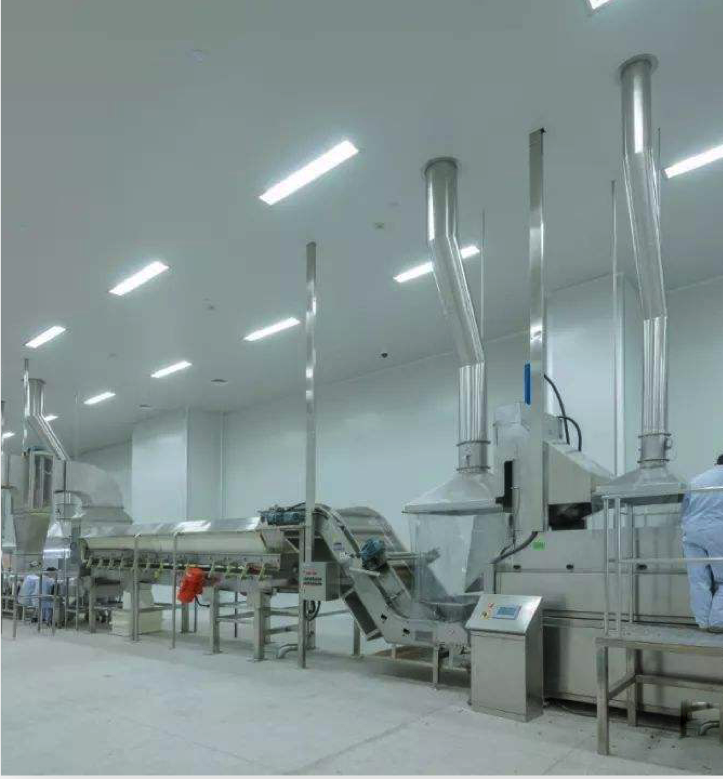
Dust pollution is a pollution problem that many production companies such as chemical industry, medicine, light industry, etc. may encounter.
Dust pollution caused by pharmaceutical companies in the production of solid preparations not only has the characteristics and hazards of general dust, but also contains the toxic hazards of medicine. Mixing of medicine or cross-contamination will occur through the purification air-conditioning system, which will also affect human health and the environment. It is also relatively large and must be effectively captured and controlled before it can be discharged after effective treatment. In particular, with the implementation of the revised Environmental Protection Law, the requirements for the treatment and emission of air pollutants have become more stringent. In environmental management, dust emissions at the boundaries of pharmaceutical factories should usually meet the comprehensive emission standards for air pollution and the concentration limits for unorganized emission monitoring, that is, ≤1.0 mg/m3.
According to the particularity of pharmaceutical production, how can its dust emissions meet the "Good Manufacturing Practice for Pharmaceuticals" (referred to as GMP) and "Pharmaceutical Industry Clean Factory Design Specifications" while achieving effective control of pollutants and environmentally friendly emissions to ensure that pharmaceuticals Improving production quality, preventing the occurrence of contamination and cross-contamination, and protecting the health of company employees are important issues that must be solved during the design and production process of pharmaceutical clean plants, and are also a vital task for engineering designers.
This article combines the actual production, starting from the dust generation link in pharmaceutical production, and discusses how to choose a reasonable, effective and easy-to-operate dust removal system in the dust operation room of pharmaceutical clean plants.
1: Which process points generate dust?
In the production of solid preparations, the processes that generate large amounts of dust and are most prone to dust flying and spreading are: weighing, crushing, sieving, granulating, drying, granulating, mixing, tableting, coating, filling and other processes.
Although in the design and selection of equipment for these processes, in order to effectively prevent the generation of dust during the production process, production equipment that meets the requirements of "GMP" has been selected, and unit equipment should work under negative pressure or in a closed environment as much as possible, and some even Dust-producing equipment is also equipped with dust suction devices and other measures, but it is still unavoidable that a large amount of dust will be generated during the feeding, unloading and equipment cleaning of each process. If effective collection, control and cleaning are not carried out, Clear, there will be mixing or cross-contamination problems through the purification air conditioning system
2: Dust removal and ventilation principles in the operating rooms
According to GMP Article 53: Dust-producing operation rooms (such as sampling, weighing, mixing, packaging, etc. of dry materials or products) should maintain a relative negative pressure or take special measures to prevent the spread of dust and avoid cross-contamination. , and easy to clean.
Generally, the measures taken for dust-generating operation rooms are as follows: First, install external dust hoods in local locations, especially for equipment that generates large amounts of dust, to achieve local dust exhaust; Second, when local dust exhaust cannot be achieved for dust sources, , the dust source equipment is isolated with enclosure facilities within a wide range, and different air purification schemes are designed according to the air cleanliness requirements of the process; third, the pressure difference between inside and outside the workshop is used to suppress the flow of airflow and prevent the spread of dust. , avoid cross-contamination and facilitate cleaning; fourth, adopt new ventilation and full exhaust measures for the production of solid preparation workshops with high drug sensitivity and drug activity.
3: Dust removal and ventilation design in operation room
After taking the above measures, the dust-laden air in the dust-producing operation room needs to be purified by dust removal equipment, and can only be discharged to the outdoors after meeting the standards. Therefore, exploring the dust removal and ventilation technology and equipment is a prerequisite for achieving dust removal and ventilation in dust-producing operation rooms to comply with relevant GMP regulations and meet environmental protection emission requirements.
3.1 Selection of dust removal equipment
When selecting dust removal equipment, in addition to considering the equipment structure and its dust removal efficiency, it should also be based on the properties of the dust (bulk density, hydrophilicity, adhesion, specific resistance and particle size) and the properties of the gas (temperature, humidity, chemical properties, etc.) and indoor and outdoor operating conditions and other comprehensive considerations.
Dust collectors can usually be divided into two types: dry dust collectors and wet dust collectors. There are two types of dry dust collectors: filter type (cartridge dust collector, bag dust collector, etc.) and mechanical type (inertial dust collector, settling chamber, cyclone dust collector, etc.).
According to practical experience, filter-type dry dust collectors are mainly used as dust collectors in solid preparation workshops of pharmaceutical factories. Commonly used ones include the following:
1) Cartridge dust collector.
Using the method of combining gravity and filter material, large particle size powder from dusty air enters the box. Under the action of its own weight, it is separated from the dusty air and settles into the dust drawer. The remaining dust particles are filtered by the filter element. Collision, hooking, static electricity and other effects are retained on the outer wall of the filter element to achieve purification purposes. At the same time, it is also equipped with an automatic pulse backflush self-cleaning device.
The cartridge dust collector has the advantages of stable technical performance, low noise, low power consumption, beautiful appearance, flexible use, small footprint, wide application range, and high dust removal efficiency (99.99%).
2) Bag dust collector.
It is a dry high-efficiency dust collector that separates and captures dust in dust-containing gas through filter materials. It is not suitable to purify dusty gas containing oil mist, condensation water and high dust cohesion, as well as smoke with explosion hazard or sparks. For example: dust removal in coating room.
3) Primary, medium and high-efficiency fan boxes.
The basic components consist of a fan, air filter, air volume regulating valve and box. Has the following characteristics:
①Capture 1~5μm particle dust and various suspended matter;
② Using hot melt process, the structure is stable and the risk of leakage is reduced;
③Large air volume;
④Small resistance;
⑤High dust holding capacity;
⑥Can be cleaned and used repeatedly;
⑦Efficiency: 60%~95%.
Disadvantages: When the amount of dust is large, the fan box needs to be cleaned manually, which greatly increases the labor of employees.
3.2 Dust collector settings
There are two basic forms of dust collector settings. One is stand-alone dust removal. That is, one piece of equipment is equipped with a dust collector, and its exhaust air can be circulated indoors, such as a separate dust collector for a tablet press.
The other is centralized dust removal. That is, multiple dust-producing equipment share one dust collector, such as the crusher and oscillating screen in the powder screen room share one dust collector. The air suction, discharge and installation in the dust-producing operation room are all in the dust removal machine room in the non-purification area. After being processed by the dust collector, it is discharged from the workshop through the exhaust port.
3.3 Selection of dust removal process system
Choosing an appropriate dust removal process system needs to be determined based on the specific production process. The general principles are: ① Set up a system when the production process is the same, the work is synchronized, the dust points are not far apart, and different dust types are allowed to be mixed and recycled or have no recycling value;
② If the dust-containing gases have different temperatures and humidity and condensation will occur in the air duct after mixing, separate systems should be installed.
3.4 Reasonable process layout
Under the condition that the workshop layout meets the relevant conditions of process production, specifications and regulations, people and logistics should be separated and not crossed as much as possible, the process route should be smooth, the logistics route should be short and quick, and there should be no backflow or detours. Reduce the flying and spreading of dust from the source and reduce mutual influence. Centrally arrange process areas with large amounts of dust and noise to facilitate dust treatment.
Project cases
Design of the solid preparation workshop of a pharmaceutical factory in Kunming.
First of all, based on the above principles and combined with the production process, we rationally layout and organize the air flow and air volume distribution. Centrally arrange the weighing and batching room, mixing room and tablet pressing room to avoid cross-contamination and facilitate cleaning; the design considers only one dust removal system and sharing a dust removal machine room; adopt local fresh air exhaust measures, and clean the air according to the process According to the requirements of the degree, the dust removal standards in other areas of the workshop are maintained by designing a purification air conditioning scheme. In accordance with the requirements of environmental management, the emission standards of the dust removal machine room meet the requirements of the unorganized emission monitoring concentration limit of "GB16297-1996 Comprehensive Air Pollution Emission Standard".
The detailed layout of the ventilation and dust removal in the solid preparation workshop of this pharmaceutical factory is shown in Figure 1.
Secondly, two different ventilation and dust removal methods were compared and selected for the dust removal process system, and finally the second method was adopted as the design solution.
Method 1: Local dust exhaust plus environmental dust removal method, see Figure 2 for details.
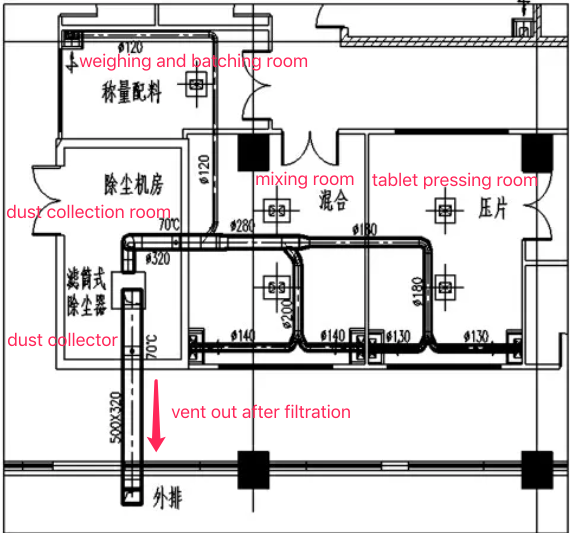
Figure 2 Partial dust exhaust plus environmental dust removal method
A dust collection hood is installed above the equipment in the dust production room for local dust exhaust. The suction hood and the inside of the dust hood are in a negative pressure state. The dust-containing gas is transported to the dust removal machine room through the negative pressure of the pipeline, and is dusted by the cartridge dust collector. After reaching the standard, it is directly discharged to the outdoor atmosphere through the chimney.
If some dust still exists in the dust-producing room environment after partial dust removal, air supply from above the dust-producing room and side exhaust are used to transport the dust-containing gas in the dust-producing room environment to the dust removal machine room through negative pressure pipes. After dust removal treatment in the medium-efficiency fan box, it will be directly discharged to the atmospheric environment through the chimney after reaching the standard.
Above the equipment in the dust-producing operation room, a dust collection hood is installed for local dust exhaust. The suction hood and the inside of the dust hood are in a negative pressure state, and the dust-containing gas is transported to the dust removal machine room through the negative pressure of the pipeline, and is dusted by the cartridge dust collector. After reaching the standard, it is directly discharged to the outdoor atmosphere through the chimney.
If some dust still exists in the dust-producing room environment after partial dust removal, air supply from above the dust-producing room and side exhaust are used to transport the dust-containing gas in the dust-producing room environment to the dust removal machine room through negative pressure pipes. After dust removal treatment in the medium-efficiency fan box, it will be directly discharged to the atmospheric environment through the chimney after reaching the standard.
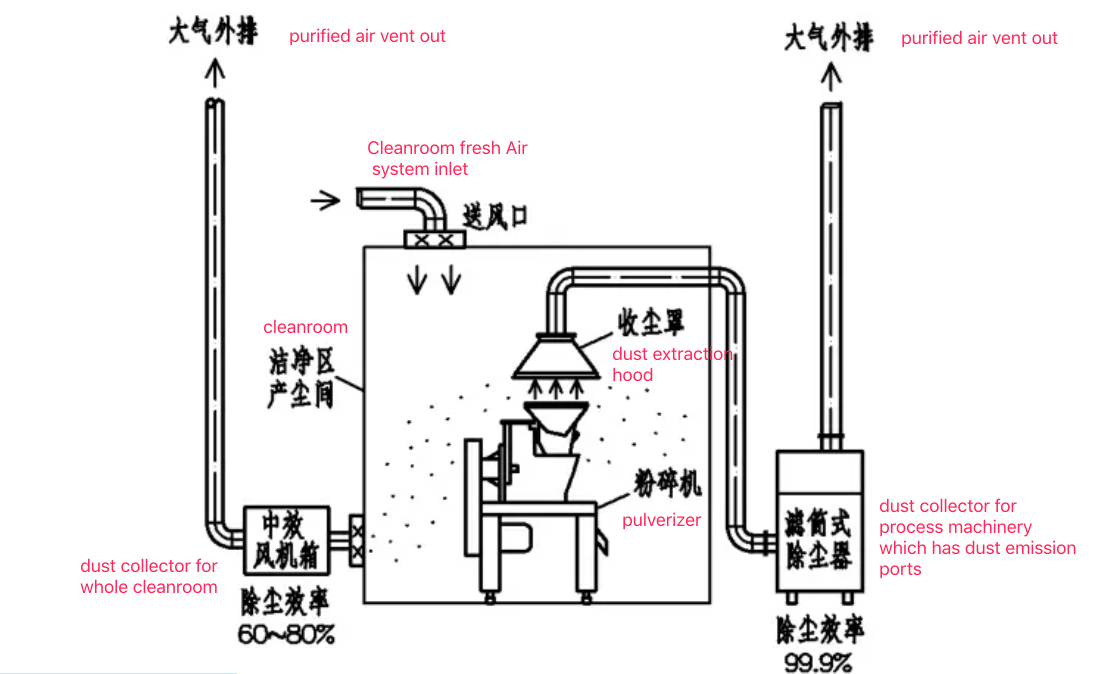
Method 2: Only environmental dust removal method is provided, see Figure 3 for details.
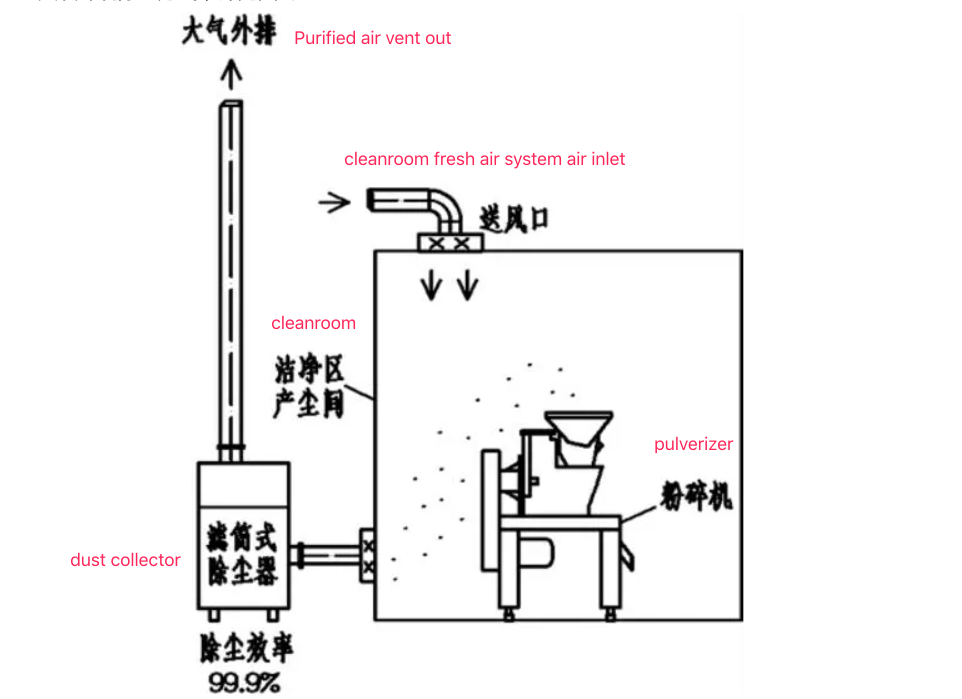
Figure 3 Only environmental dust removal method
Dust removal is only carried out for the space environment in the dust-producing operation room, and no local dust exhaust is performed. That is: increase the air supply and exhaust volume, and still use air supply from above the dust-generating operation room. The side exhaust method transports the dust-laden gas in the dust-producing operation room to the dust removal machine room through negative pressure pipes, where it is removed by the cartridge dust collector and then directly discharged to the outdoor atmospheric environment through the chimney.
The choice of method two in this case is mainly determined based on the production process and the amount of dust generated by the specific process. Compared with method one, method two has the characteristics of short process, easy adjustment of air pressure and air volume in the clean area of the workshop, and simple process operation. At the same time, the cartridge dust collector is equipped with an automatic pulse backflush dust cleaning device, which has high dust removal efficiency. The equipment is also arranged to operate in a non-clean area, which can save labor costs and reduce energy consumption.
The design scheme has been proven in practice that the dust removal effect is very obvious, which not only meets the requirements of the new version of GMP, but also meets the requirements of the unorganized emission monitoring concentration limit of the comprehensive emission standard of air pollution.
Conclusion
The production dust in the dust operation room of a pharmaceutical clean factory has its own uniqueness. The two dust removal process systems in this case are often used in the design, each with its own advantages and disadvantages. The key is to fully understand the properties of dust and gas at each dust generation point and the operating conditions, flexibly choose economical and applicable dust removal measures, and design the best dust removal plan.