How To Design Dust Extraction System for Multi Dust Emission Points-Tablet Coating Pans As Example?
- Share
- Issue Time
- Mar 15,2024
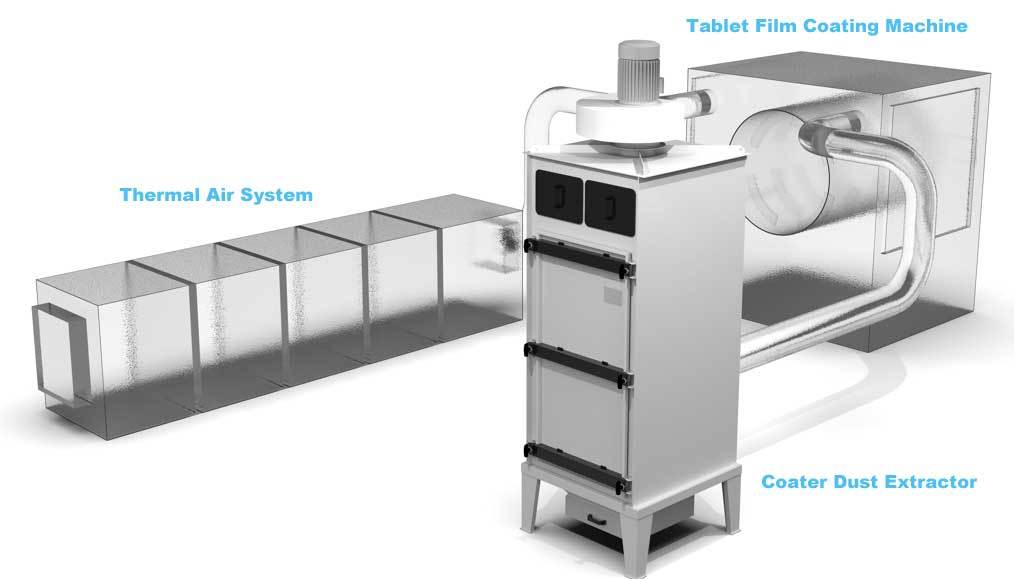
How To Design Dust Extraction System for Multi Dust Emission Points-Tablet Coating Pans As Example

The production workshop of a pharmaceutical factory has a construction area of about 3240m². It is a single-story building with partial 2 floors. The building height is about 10m. The indoor ceiling height is 2.7m. The upper part is the equipment pipeline layer, and the partial 2-story building is the air-conditioning machine room. Area H is the sugar coating packaging workshop with a total of 12 sugar coating machines.
During the pharmaceutical production process in the sugar-coating workshop of a pharmaceutical factory, a large amount of process talc dust will escape, and effective dust removal measures need to be taken. If dust removal measures are not handled properly, the dust will pollute the indoor air, block and contaminate the purification air-conditioning system, affect the physical and mental health of the staff, thereby destroying the requirements for a clean production environment in the production room and the quality of pharmaceuticals;
And it causes pollution to the outdoor atmospheric environment.
Energy Saving Consideration
Since the dust generation points of process dust are concentrated near the process equipment in the clean room, in order to save energy (such as purifying air conditioning system energy: power supply, exhaust, cooling, heat load, etc.) and saving production space, the layout of the production process is generally considered. , the area of the dust-producing production area should be minimized. Therefore, the room ventilation air volume per unit time is smaller (relatively
For the dust removal system, the available exhaust air volume is also small, and it is necessary to reasonably select the air volume, wind speed, dust collection device and dust removal equipment).
Local ventilation is is better than whole room ventilation
External suction hood. When the production equipment cannot be sealed due to limitations of process conditions, the exhaust hood can be placed near the source of harmful substances. The suction effect of the hood can be used to create a certain air flow at the point where the pollution source emanates, and the harmful substances can be removed. Suction into hood.
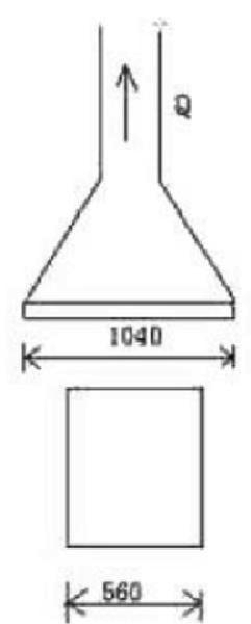
In this design, the pollution source produces light mineral talc dust, which disperses into the above-mentioned calm air at a slight speed. Therefore, the control speed of the pollution source can be obtained from the control air speed table of the control point in "Industrial Ventilation", which is 0.5m/s~1.0 m/s. This design uses v=0.6m/s.
Determination of exhaust volume and size of suction hood
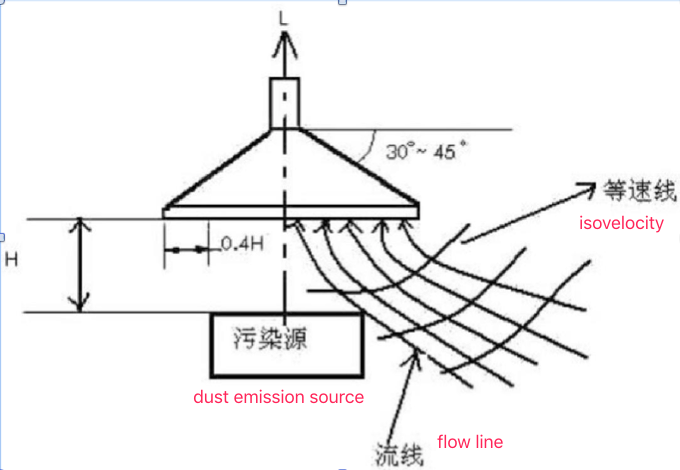
1): Top Design
The exhaust hood is located above the sugar coating machine. Due to equipment limitations, gas can only flow into the hood from the side, as shown in Figure 3.2. In order to avoid cross-air flow interference, it is required that H should be ≤0.3L as much as possible (the long side dimension of the cover mouth), take H=0.4m, therefore, L≥1.33m, take L=1.4m.
2): Suction hood size:
The diameter of the umbrella-shaped suction cover is: 0.56+2×0.4H=0.56+2×0.4×0.4=0.88(m)
The perimeter of the suction hood is: 3.14×0.88=2.76(m)
3) In order to ensure the uniform inhalation speed of the mask mouth, a is set to 60° in this design.
4) The exhaust air volume is calculated according to the following formula:
Q=KPHvx
=1.4×2.76×0.4×0.6
=0.93(m²/s)=3348(m³/h)
In the formula: P --- perimeter of the open surface of the hood, m;
H---- distance from the mask mouth to the pollution source, m;
vx-----Control speed, m/s;
K----Considering the uneven velocity distribution along the height, the safety factor is usually taken as K=1.4.
Pipe design
First, design the layout position of the pipeline, then number each pipe section, and select the calculation loop according to the principle of maximum pressure loss.
Determination of the minimum speed in the pipeline
In this design, the pollutant is light mineral powder. According to the "Ventilation and Dust Removal Equipment Design Manual", the minimum flow velocity in the horizontal pipe is 14m/s and the vertical pipe is 12m/s.
Minimum air flow velocity in dust removal ventilation duct (m/s)
Dust properties | Vertical pipe | Horizontal Pipe | Dust properties | Vertical pipe | Horizontal Pipe |
m/s | m/s | ||||
Powdered clay and sand | 11 | 13 | Iron and steel (chips) | 19 | 23 |
Fire clay | 14 | 17 | dust | 16 | 18 |
heavy mineral dust | 14 | 16 | sawdust, chippings | 12 | 14 |
light mineral dust | 12 | 14 | Large dry sawdust | 14 | 15 |
dry sand | 11 | 13 | dry dust | 8 | 10 |
coal ash
|
10
|
12 | fuel dust |
14-16
|
16-18
|
Wet soil
(less than 2% moisture) |
15 |
18 | Large pieces of wet sawdust |
18 |
20 |
Iron and steel (dust)
|
13
|
15 | grain dust |
10
|
12
|
cotton
|
8
|
10 | Hemp, short fiber dust |
8
|
12
|
Pipe material Choosing
In the dust removal system of a pharmaceutical factory's clean room, materials such as pipes and fittings and valves should be selected based on the physical and chemical properties of the materials being transported and the working conditions. The materials and valves used should meet the process requirements and should not adsorb or pollute the media. The exposed pipelines introduced into the medical clean room (area) should be made of stainless steel or other materials that do not pollute the environment. Air ducts in pharmaceutical factories are usually made of SUS materials (high-quality galvanized steel plates can also be used). The material thickness is determined according to the corrosiveness and abrasion of the dust. For smaller dust removal systems, a plate thickness of 1.2mm to 2mm is generally sufficient. This design uses thin steel plate because its advantages are that it is easy to be processed and manufactured industrially, easy to install, and can withstand higher temperatures.
Selection of air duct cross-section shape
The cross-sectional shapes of air ducts are round and rectangular. Compared with the two, when the cross-sectional area is the same, the circular air duct has less resistance, saves material, and has greater strength; when the diameter of the circular air duct is smaller, it is easier to manufacture and is more convenient for thermal insulation. However, it is more difficult to lay out and make circular air duct fittings than rectangular air ducts; it is not easy to coordinate with the building and structure when laying out, and it is not easy to arrange beautifully when exposed. When the flow velocity in the air duct is high and the diameter of the air duct is small, a circular air duct is usually used, so a round air duct is selected here.
The flow rate in the air duct should be determined from both technical and economic aspects. Judging from the actual engineering situation, it is appropriate to choose a lower flow rate (selectable lower limit of flow rate) for the dust removal system in the pharmaceutical factory's clean room, and should be combined with reasonable air duct layout, which can save energy consumption. With appropriate technology, it will not Cause dust precipitation and blockage. After the flow rate and flow rate of the air duct are determined, the cross-sectional size of the duct can be calculated as follows:
Q=(π d²V)/4 gets:
d=√4Q/πV
d—Duct diameter m
Q—Dust gas flow rate m³/s
V—dust gas flow velocity m/s
Determination of elbow
When laying out pipes, try to keep straight lines and reduce elbows. The radius of curvature of circular air duct elbows should generally be greater than (1~2) times the pipe diameter. Therefore, a 90° elbow is taken here. Due to the erosion and wear of the elbow by the dusty airflow in the pipeline, it is easy to wear through and leak air, which affects the normal dust collection effect. Therefore, wear-resistant facilities must be installed on the elbow.
Determination of three links
The collision between two airflows with different flow speeds in the tee and the formation of vortices when the airflow speed changes causes local resistance. In order to reduce the local resistance of the tee, the ejector phenomenon should be avoided, and attention should be paid to the connection between the branch pipe and the main pipe to reduce the angle. Therefore, the angle between the branch pipe and the main pipe is a=30; at the same time, the branch pipe should also be as close as possible to the main pipe. Maintain the same flow rate as the flow rate in the main pipe. Like elbows, tee fittings should also be equipped with wear-resistant facilities.
Using 30° converging tee: resistance coefficient ξ=0.20 force coefficient ξ=0.18.
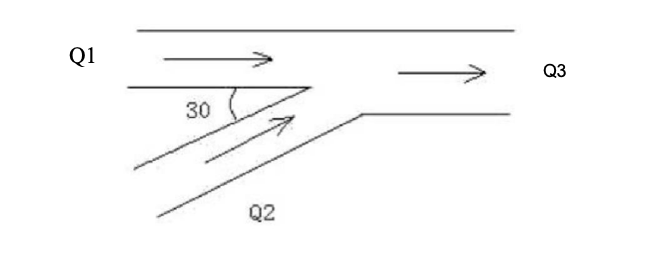
Then use a "Pipe pressure calculator" App to calculate the pressure loss. If you do not have, please ask ACMAN for help:
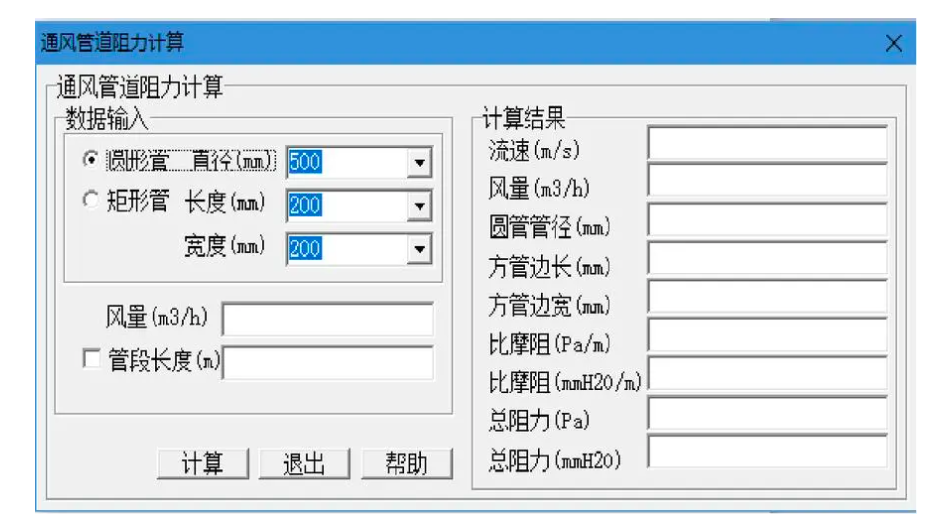
Dust Collector Choosing
When selecting a dust collector, the properties and particle size distribution of the dust, the temperature and properties of the gas, and the dust concentration of the gas should be considered.
Factors such as the degree of dust removal and the problem of handling dust removed by the dust collector.
The properties of dust have a great influence on the performance of the dust collector. For example, dust with greater viscosity is easy to adhere to the surface of the dust collector and is not suitable for dry dust removal; dust with too large or too small specific resistance is not suitable for electrostatic dust removal. When dealing with abrasive dust, the bag dust collector should use wear-resistant filter media. Different dust collectors have completely different dust removal efficiencies for dust with different particle sizes.
Similarly, when choosing a dust collector, you must first understand the particle size distribution of the dust to be processed and the classification efficiency of various dust collectors.
During the sugar-coating packaging process in the sugar-coating workshop, talc dust will be emitted, affecting the personal health of employees and the air quality in the workshop. In severe cases, the accumulation of a large amount of dust may cause an explosion and affect production. Therefore, the dusty air needs to be purified after being collected. Allowed to vent to atmosphere. Since the collected talc dust has a small particle size between 0.5 and 1.0 μm, and it also contains certain medicinal ingredients, it needs to be recycled. The cartridge dust collector has an efficiency of up to 1.0 μm for dust.
98%~99%. Therefore, the choice of cartridge dust collector has a small footprint and high cost performance.
Blower Choosing
Select the appropriate fan and motor based on the air volume and total resistance of the system.
1) Determine the type of fan based on the properties of the transported gas, the air volume and resistance of the system.
This fan transports talc dust. Due to the fluidity of the dust, static electricity will be generated and cause an explosion. Therefore, an explosion-proof fan is selected.
2) Taking into account the air leakage and resistance calculation of air ducts and equipment, the air volume and air pressure should be selected according to the following formula:
machine:
Pf=KpΔP (Pa)
In the formula, Pf——the wind pressure of the fan;
Kp additional coefficient of wind pressure, general air supply and exhaust system Kp=1.1~1.15; dust removal system Kp=1.15~1.20;
ΔP——the total resistance of the coefficient;
LF=KLL (m³/h)
In the formula,LF—the air volume of the fan;
KL——Additional coefficient of air volume, general air supply and exhaust system K₁=1.1; dust removal system K₁=1.1~1.15
L——The total air volume of the coefficient.
Fan wind pressure Pf=KpΔP=1.15×1609.3=1850.7Pa
Fan air volume LF=KLL=1.15×42336=48686.4m³h
select 4-68No.10 fan, its performance is
Pf=2030 Pa LF=49040 m3/h
Fan speed: n=2300r/min.
Equipped with YZ25S-4 motor, the power of the motor is N=40KW.
Conclusion
At last, You can Find the suitable dust collector in ACMAN product list: