Sinter Lameller Filter, Herding Gmbh Pure Surface Filter, De-Dusting Sinter Filters, Herding Delta2 750/9, Aritikel Nr S-20543
- Model
- Herding Delta2 Sinter Lameller Filter
Review
Description
Sinter Lameller Filter technology bases on pure surface filtration. It sustainably protects man and machine from harmful production emissions and enables absolutely sort- and contamination-free material recovery. This increases directly your productivity.
Lowest clean gas values, absolutely constant operating conditions, highest availability and energy efficiency are key features of the innovative technology. Sintered PE Surface filter elements show extreme durability and, depending on the process, long service life times of more than 15 years. Thereby the filters make a valueable contribution to environmental protection and sustainability.
Sintered PE Surface filter elements have proven themselves for decades in effective and safe particle separation in almost all areas of industry . Even with finest grain sizes, energy-efficient air recirculation is possible in most cases, proven even with toxic dust.
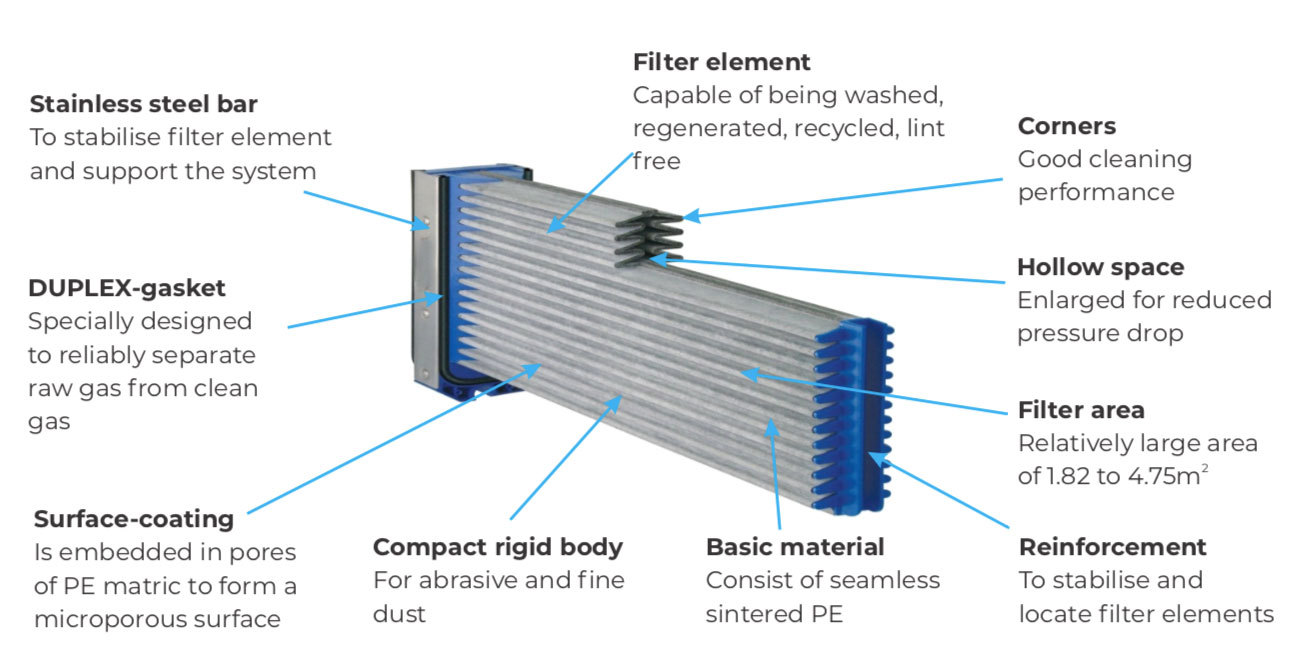
Sinter plate filter | Advantages |
Pure surface filtration due to PTFE embedded in the PE-matrix and non-flexible filter media
|
No penetration and deposition of dust particles in pores
|
Rigid body design | No wear and tear on the media due to movement (contraction during suction, expansion during cleaning) Long operational life time up to 10 years possible Low maintenance costs Filter elements can not fall down into the silo due to screwed mounting and no breaking of elements No tearing of element possible |
Two screw mounting system and lower number of elements |
Quick change of filter elements without the need for extra equipment (crane) |
Perfectly suited for product recovery as medium is free of lints or fibres that could get loose |
no danger of textile getting loose and contaminating the product
|
Sinter-plate filter advantage:
l Filter element lifetime of up to 15 years possible
l Low maintenance costs due to long useful life of the filter elements
l Constant pressure drop guarantees consistent air flow
l High separation efficiency due to surface filtration
l Clean gas emissions <1.0 mg/m3
l Compact rigid body generates a robust filter design
l Filter medium: capable to be washed, recycled and refurbished
l Universal mounting from the raw- or clean gas side of the filter unit
l Horizontal or vertical installation possible
l Filter medium absolutely free of fibers, ideal for product recovery
l Excellent use for highly abrasive dusts
l Antistatic version of the filter elements available
l FDA-conformity by using food-grade filter material

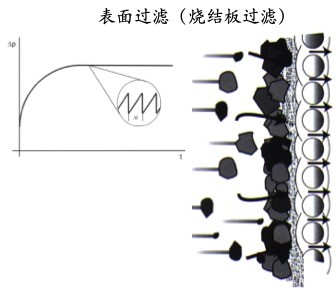
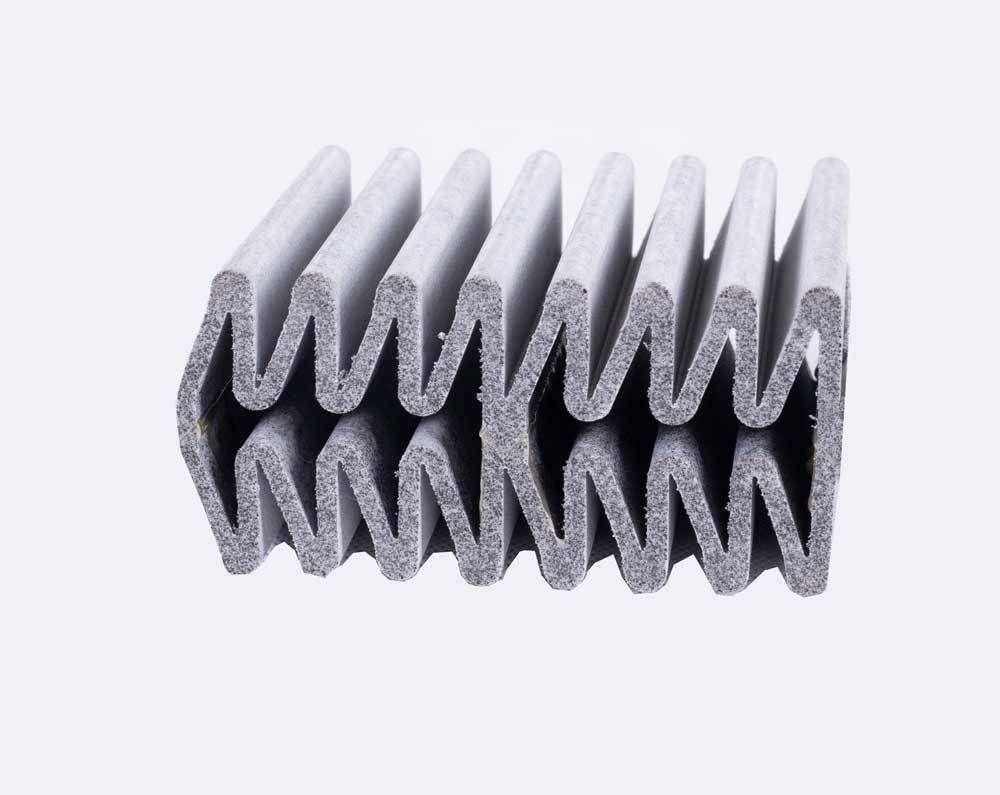
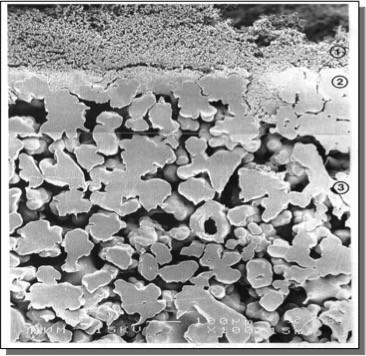
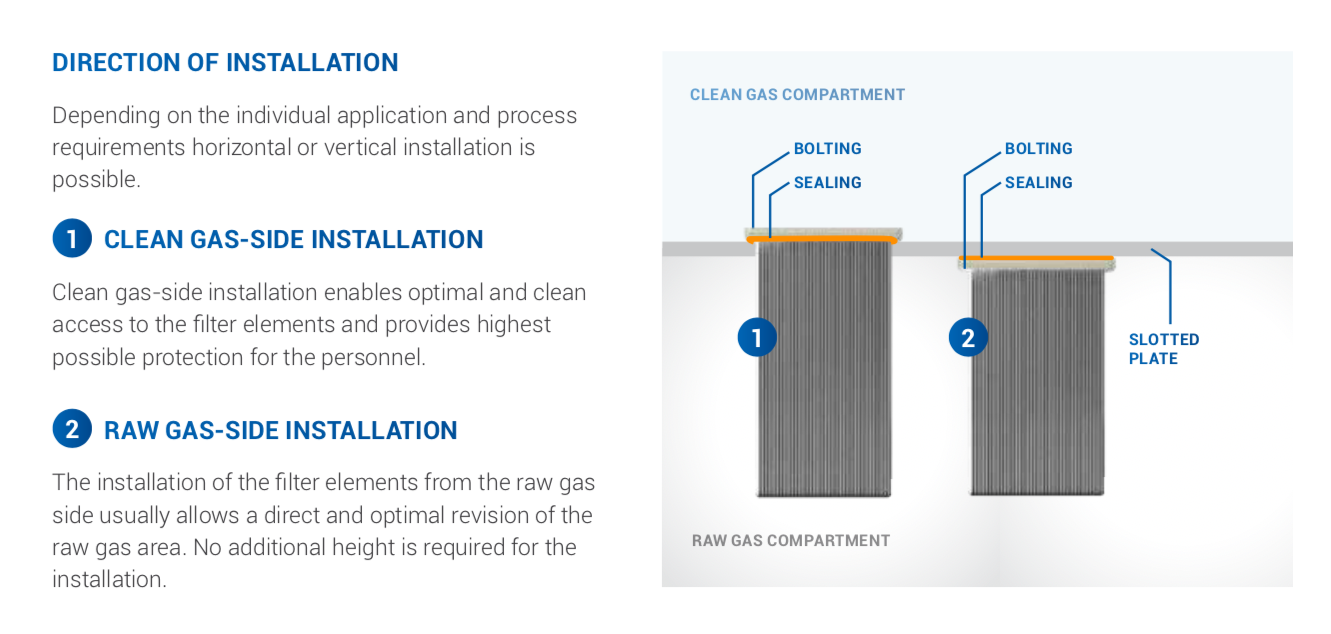
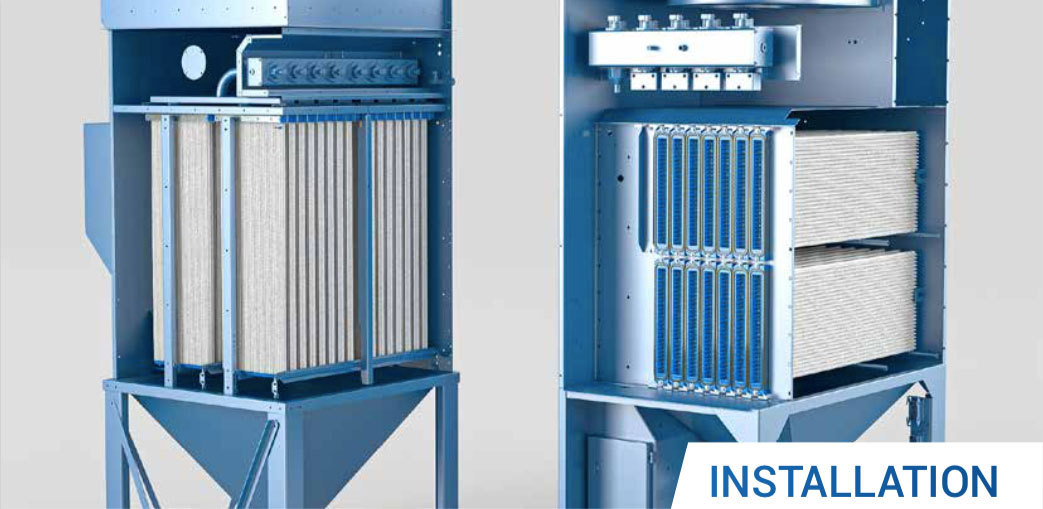
Model
|
L (mm) | W (mm) |
D (mm)
|
Filter Area (m2)
|
Weight (kg)
|
Delta2 500 | 533 | 564 | 80 | 1.57 | 4.8 |
Delta2 750
|
767 | 564 |
80
|
2.34
|
6.3
|
Delta2 1000
|
1023 | 564 |
80
|
3.18
|
7.9
|
Delta2 1500
|
1504 | 564 |
80
|
4.75
|
10.9
|
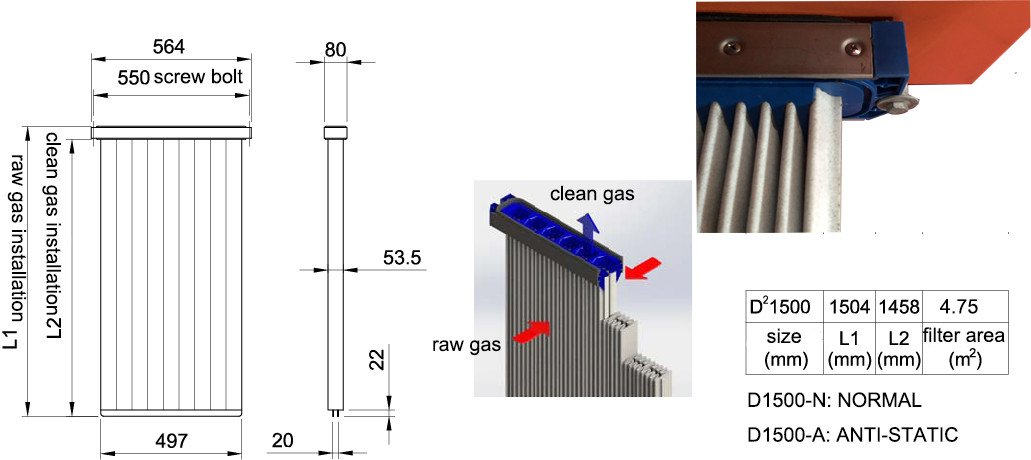
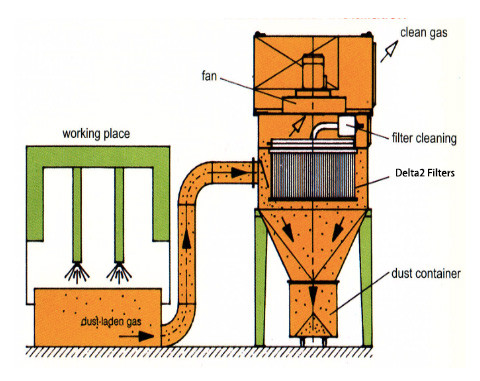
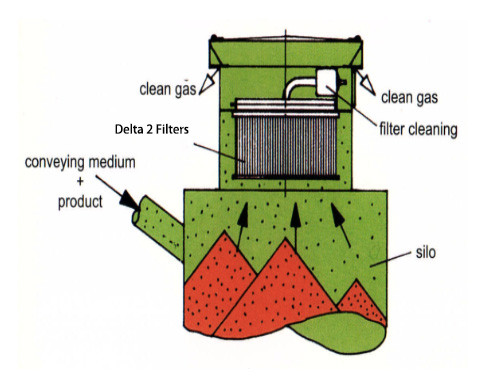
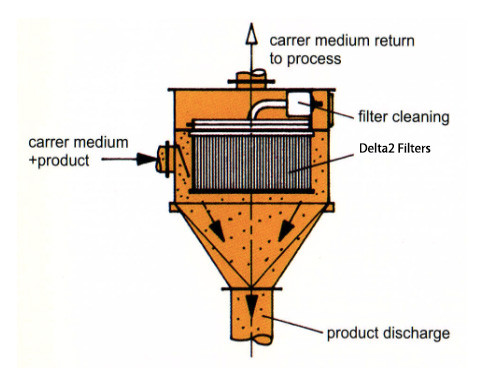
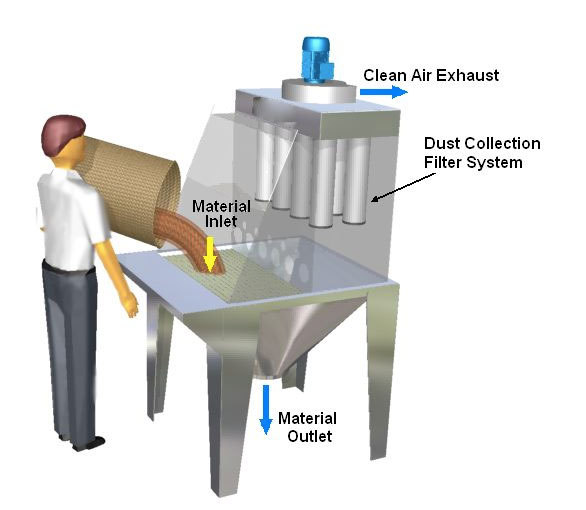
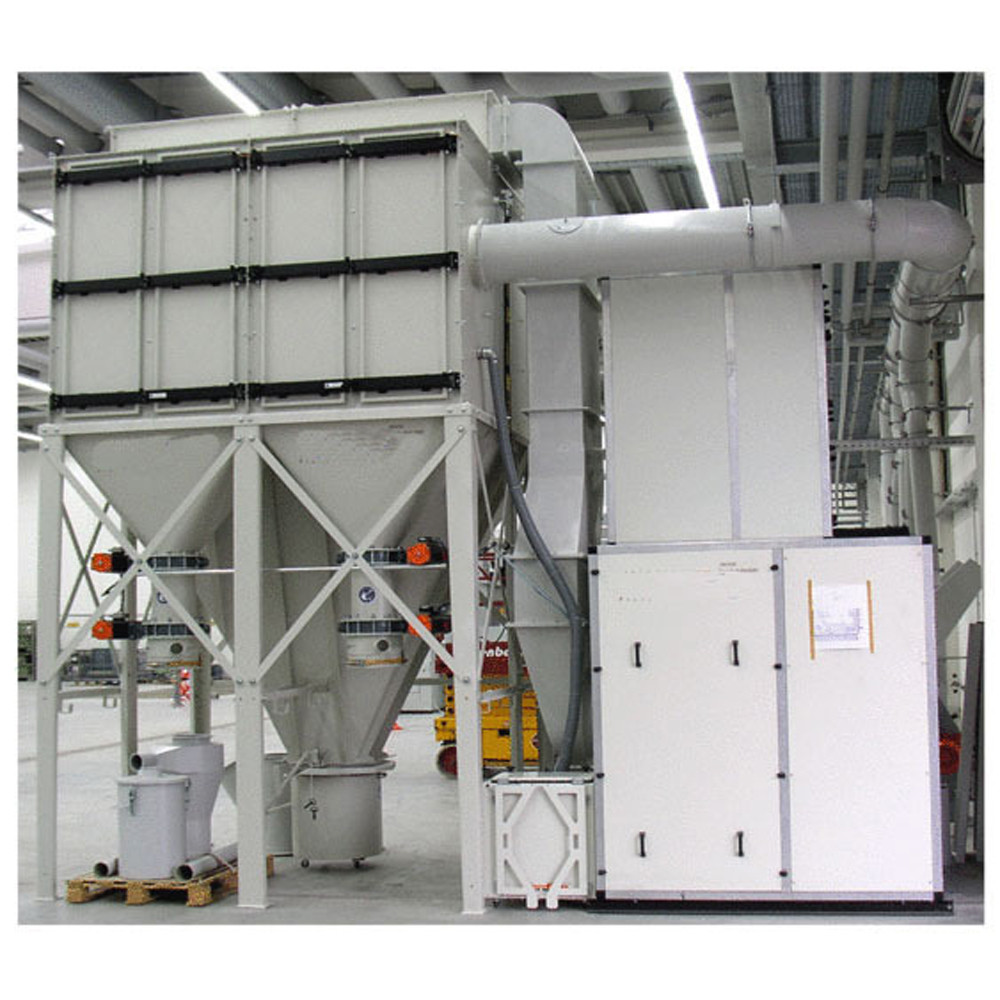
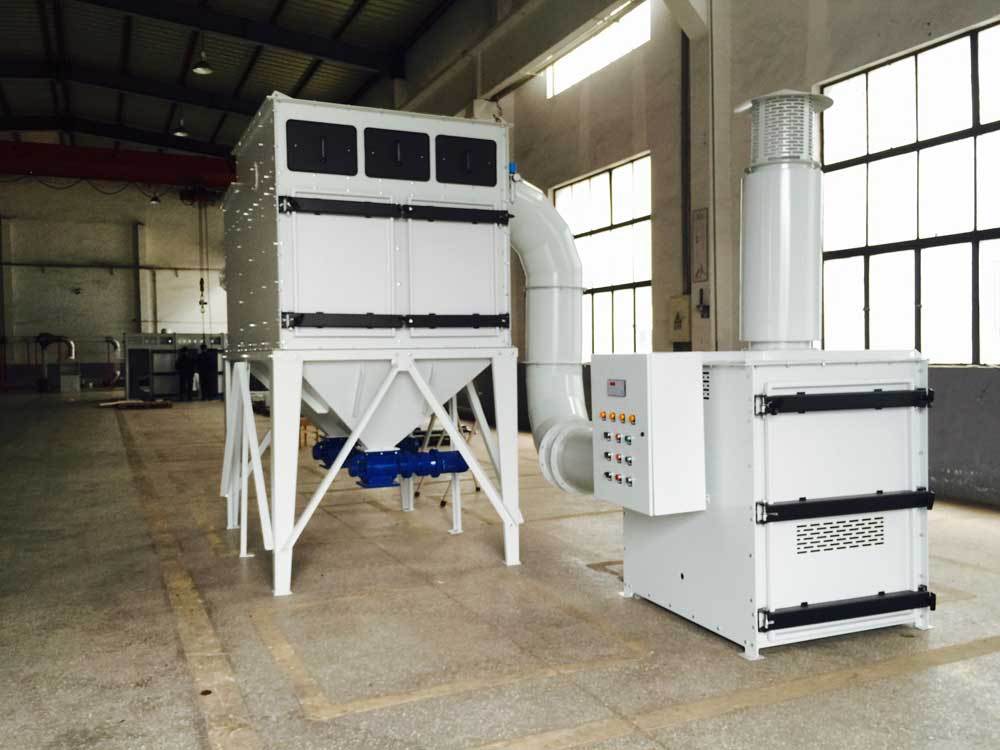
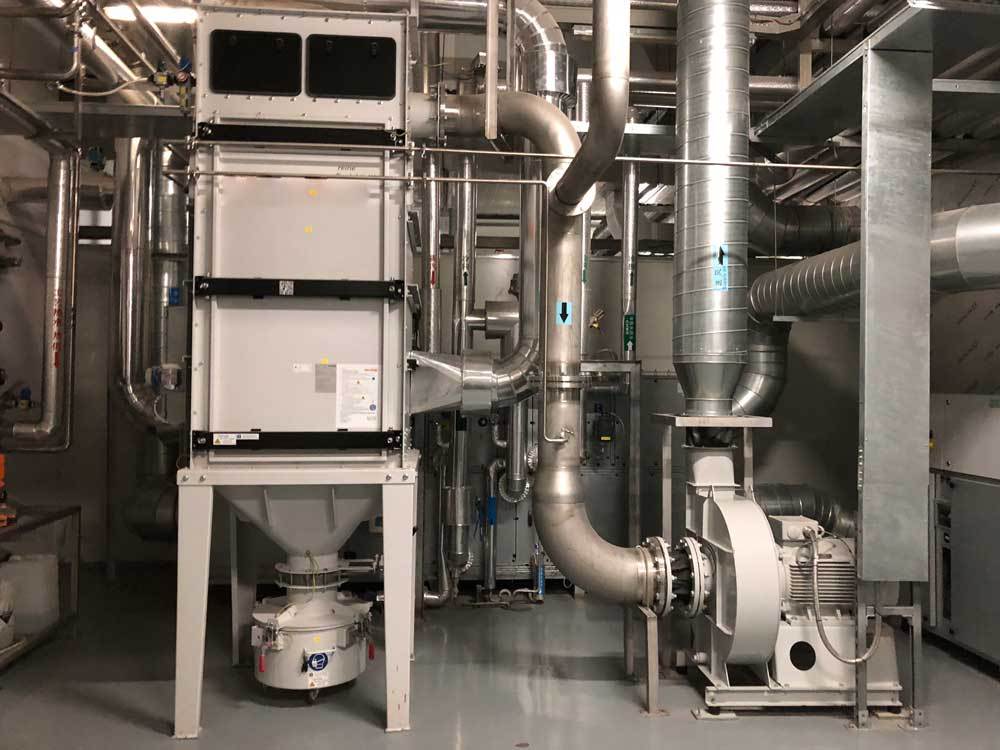
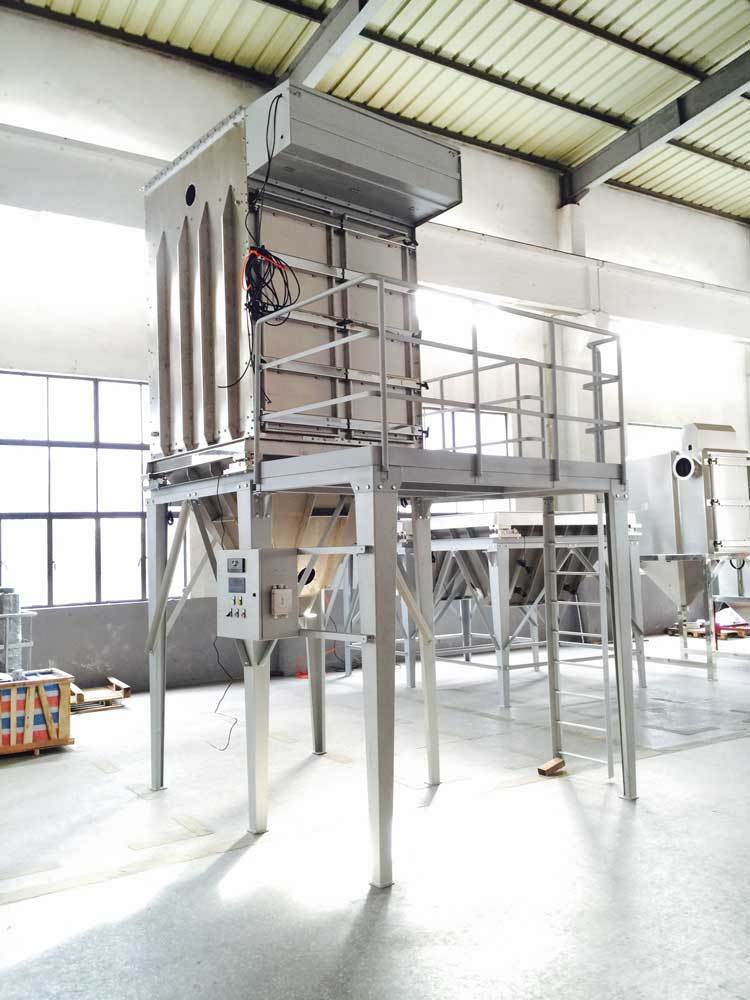
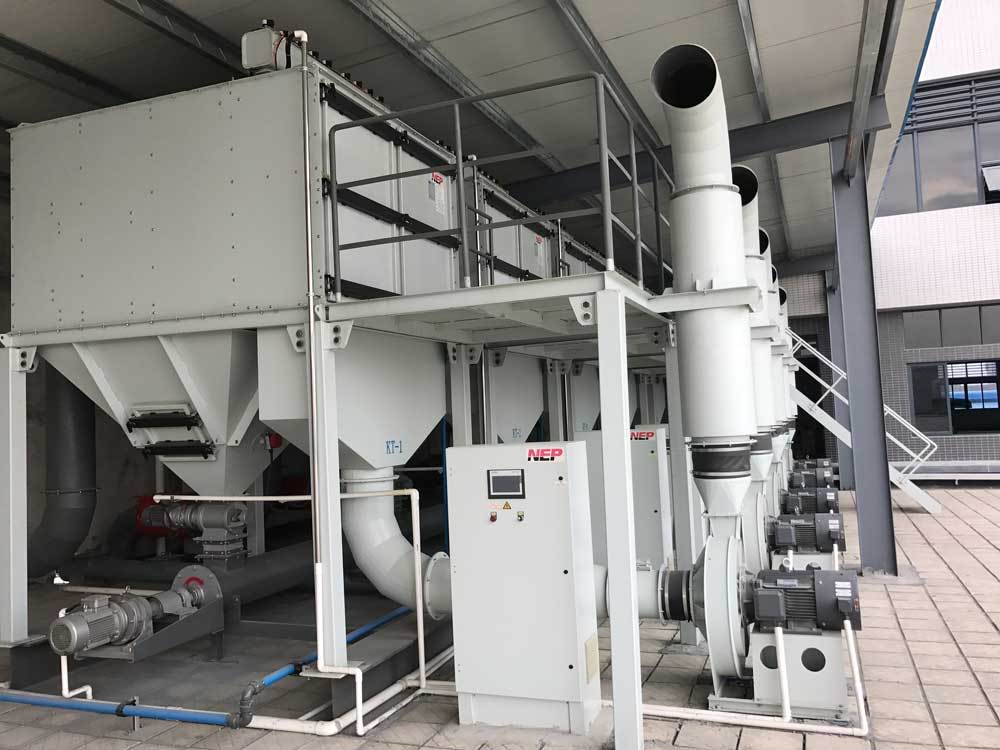
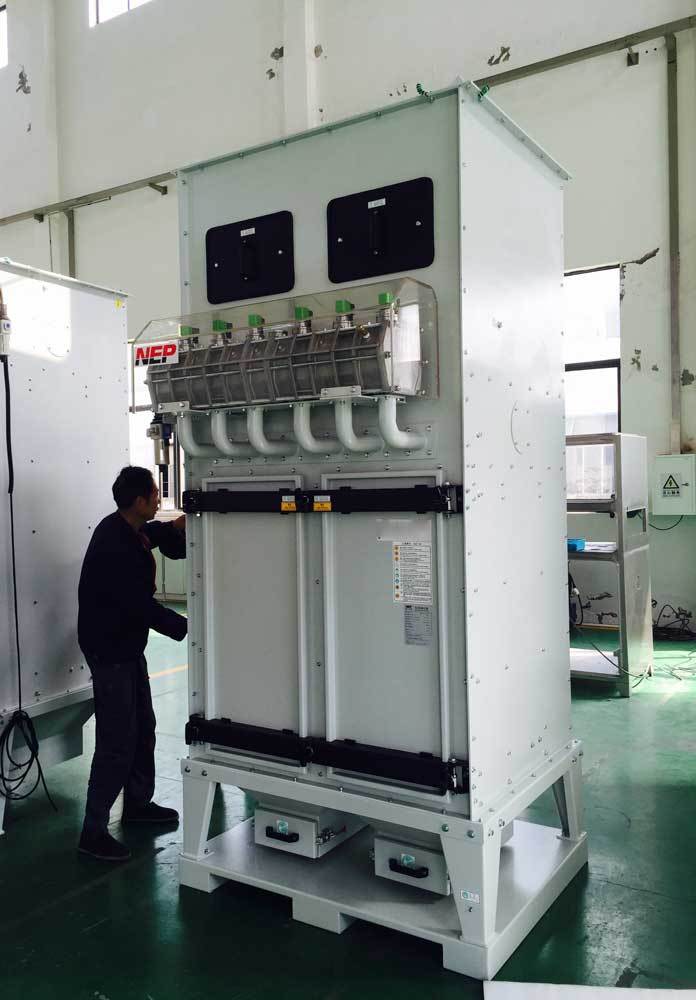